Unveiling the Art and Science of Thermoset Moulding Compounds: Crafting Excellence in Engineering
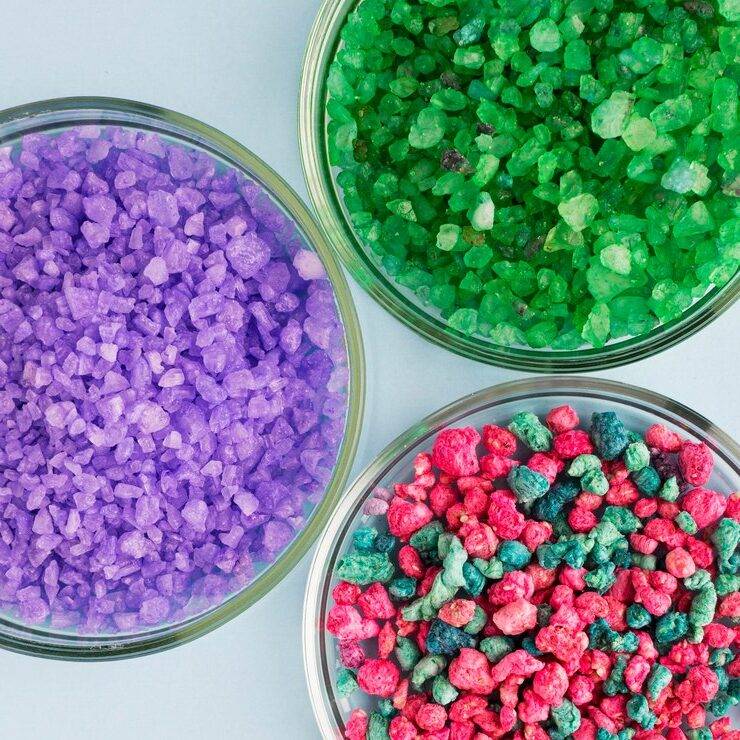
In the realm of advanced materials, thermoset moulding compounds stand as a testament to the fusion of science and craftsmanship. These compounds, characterized by their resilience and versatility, play a pivotal role in shaping the future of engineering across diverse industries. Let’s delve into the intricacies of thermoset moulding compounds and explore their myriad applications.
Understanding Thermoset Moulding Compounds:
1. Composition:
Thermoset moulding compounds are composite materials composed of a polymer resin matrix, reinforcing fibers, and additives. The polymer resin undergoes a chemical reaction during the moulding process, creating a cross-linked, three-dimensional network that imparts exceptional strength and stability.
2. Diverse Formulations:
These compounds come in various formulations to cater to specific application requirements. Common resin matrices include epoxy, phenolic, melamine, and polyester, each offering unique properties suited for different industries and use cases.
The Moulding Process:
1. Compression Moulding:
In compression moulding, thermoset compounds are placed in a mould cavity and subjected to heat and pressure. The resin undergoes polymerization, resulting in the desired shape and properties. This method is widely used for components requiring high strength and dimensional accuracy.
2. Injection Moulding:
Injection moulding involves injecting molten thermoset material into a mould under high pressure. This process is ideal for intricate and detailed components, offering precision and efficiency in large-scale production.
Applications Across Industries:
1. Automotive Advancements:
Thermoset moulding compounds find extensive use in automotive manufacturing. From lightweight components in vehicle interiors to high-strength under-the-hood applications, these compounds contribute to enhanced performance and fuel efficiency.
2. Electrical and Electronics:
The electrical and electronics industry benefits from the excellent insulating properties of thermoset moulding compounds. They are integral to the production of circuit boards, electrical enclosures, and insulating components, ensuring reliability and safety.
3. Aerospace Excellence:
In the aerospace sector, the demand for lightweight, high-strength materials is met by thermoset moulding compounds. From structural components to interior elements, these compounds play a critical role in achieving the stringent performance requirements of the aerospace industry.
Advantages and Future Trends:
1. Exceptional Strength-to-Weight Ratio:
Thermoset moulding compounds offer an outstanding strength-to-weight ratio, making them ideal for applications where weight reduction without compromising strength is crucial.
2. Customization and Innovation:
Ongoing research and development in thermoset technology allow for the customization of formulations, enabling manufacturers to tailor materials to specific performance criteria. This flexibility drives innovation across industries.
Read More from our latest Study on Molding Compound Market Based On Resin Type, Application, And Region – Global Forecast Up To 2030.
Conclusion:
As we navigate the dynamic landscape of modern engineering, thermoset moulding compounds stand as stalwarts of innovation. Their ability to blend strength, durability, and customization options positions them as indispensable materials in the pursuit of excellence across automotive, aerospace, and electronics sectors.
– Analyst Team
IHR Insights
inquiry@ihrinsights.com