Non-Destructive Testing and Inspection (NDT & I): Ensuring Structural Integrity and Safety
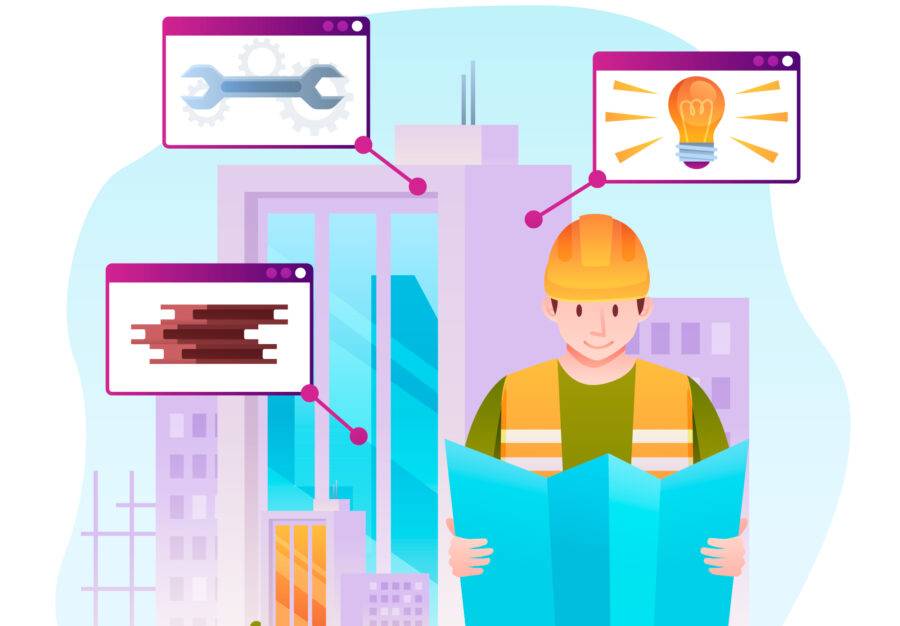
Non-destructive testing and inspection play a crucial role in verifying the integrity of materials, components, and structures without causing damage. These methods are essential in various industries, including aerospace, manufacturing, and infrastructure. Let’s delve into the diverse methods of NDT & I and their vital significance in ensuring safety and reliability.
Visual Testing (VT)
Visual inspection is the most fundamental form of NDT, involving direct visual examination to detect surface irregularities, corrosion, or other visible defects. It remains a critical initial step in assessing the condition of materials and structures.
Liquid Penetrant Testing (PT)
PT involves applying a liquid penetrant over the surface of a material, allowing it to seep into surface-breaking defects. After a developer is applied, the penetrant’s presence is revealed, aiding in the detection of cracks, porosity, and leaks.
Magnetic Particle Testing (MT)
MT is employed to identify surface and near-surface flaws in ferromagnetic materials. By inducing a magnetic field and applying iron particles, defects become visible, enabling precise flaw detection in magnetic materials.
Radiographic Testing (RT)
RT employs X-rays or gamma rays to create an internal image of a component on film or digital media. It’s effective for detecting internal defects and assessing material thickness, especially in weld inspections and heavy castings.
Ultrasonic Testing (UT)
UT uses high-frequency sound waves to assess internal and surface conditions. Sound waves are emitted, and the reflections are analyzed to identify defects, measure material thickness, and evaluate material properties with high precision.
Eddy Current Testing (ET)
ET is designed for conductive materials, utilizing electromagnetic induction to detect surface and near-surface defects. It’s particularly effective for flaw detection and material sorting in non-ferromagnetic materials.
Thermographic Testing (TT)
TT relies on thermal imagery to identify structural irregularities by detecting variations in thermal patterns. It’s valuable for assessing material homogeneity, composite structures, and detecting subsurface defects.
Acoustic Emission Testing (AE)
AE involves monitoring the structural response to an applied stress, detecting transient stress-induced acoustic waves. This method is utilized for identifying active flaws and assessing ongoing material degradation.
Read more from our Non-Destructive Testing And Inspection Market Study By Test Method (Traditional NDT Method, Digital/Advanced NDT Method), By Offering, By Vertical, By Regional Outlook.
Conclusion:
Non-destructive testing and inspection methods are essential for identifying flaws, defects, and irregularities while ensuring the integrity and safety of critical components and structures. These techniques, in combination with industry-specific standards and regulations, enable the reliable assessment of materials and assets, contributing to enhanced safety, reduced downtime, and cost-effective maintenance practices.
As technology and methodologies continue to advance, the role of NDT & I becomes increasingly pivotal in upholding structural integrity, quality control, and the overall reliability of industrial assets and infrastructure.
– Analyst Team
IHR Insights
inquiry@ihrinsights.com